ich hab mich mal wieder mit meinem Lieblingsmaterial beschäftigt:
40x40 Vierkant...das sind Dimensionen wo man richtig müde wird ohne Lufthammer und alleine

Eigentlich brauch ich kein Sperrhorn, ich hab schon ein kleines. Es liegt vielleicht daran dass es nicht das beste ist aber ich benutzte es nicht allzu oft.
Ich hatte schon vor einiger Zeit die Idee mir mit meinem Kumpel Jakob zusammen ein Sperrhorn aus nem 50ger Rund zu schmieden. Allerdings hat allerdings aus verschiedenen Gründen nicht geklappt.
Also hab ich´s jetz am letzten Wochenende allein umgesetzt.
Im Prinzip ist das als würde man einen großen Nagel Schmieden.
Bei Bedarf erklär ich den Herstellungsprozess auch gerne noch im Detail.
Ausgangsmaterial war einfach nur ein "Klotz" C45, 40x40x150mm
Naja und das ist bei rumgekommen:
Unten ist es auf 25ger Vierkant geschmiedet, damit man es in die Lochplatte einsetzten kann. Extra um 45° gedreht, da dass 25ger Loch an der Ecke der Lochplatte sitzt und so beide Hörner ein wenig überstehen. Der Mittelteil ist auf 35mm Rund gechmietet. Die Hörnerspitzen liegen jeweils etwa 10 cm von der Mitte entfernt.
Und Bilder hab ich natürlich auch gemacht:
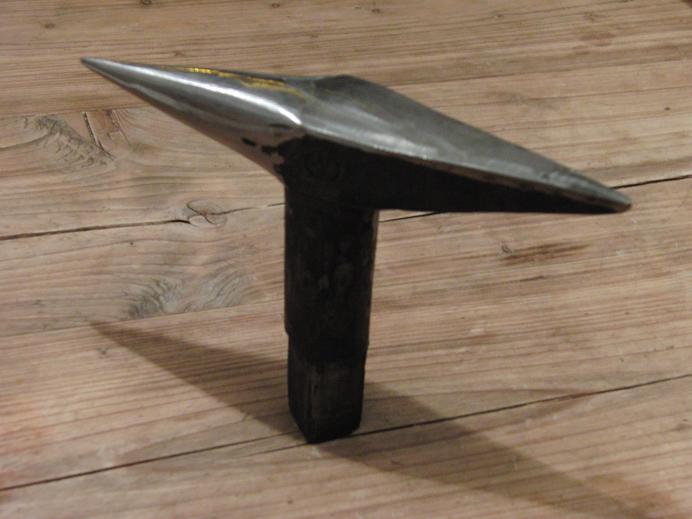
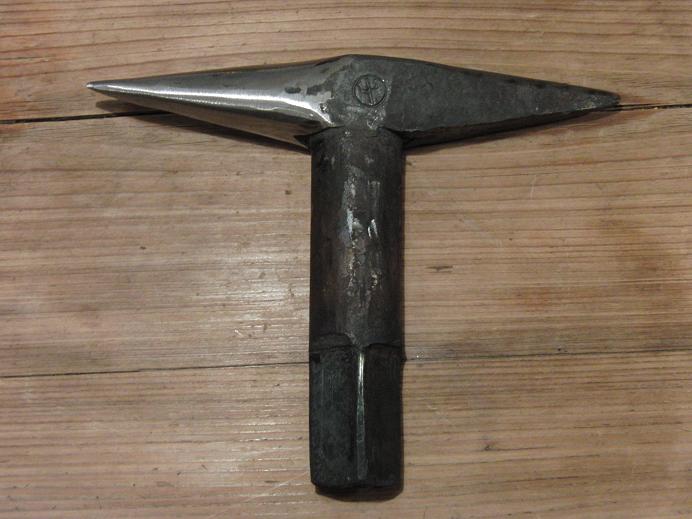
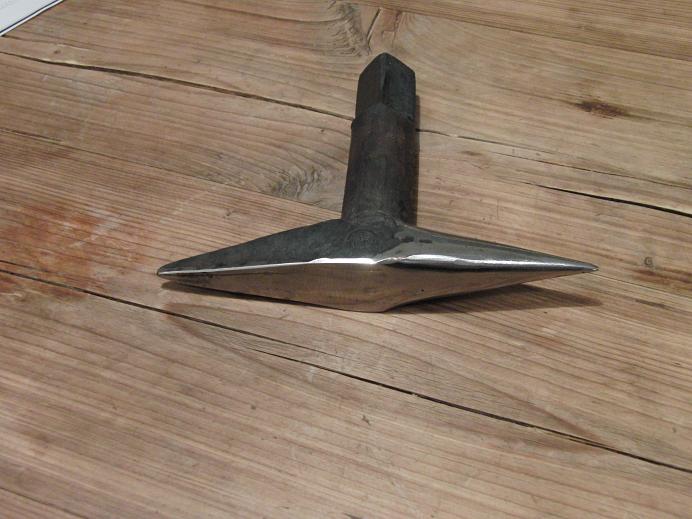
Ich hab das teil jetzt nur normalisiert.
Was sagt ihr? Härten oder nicht? wenn ja, was für Anlasstemperaturen?
Gruß
Willi